CNC machines have revolutionized manufacturing with their precision and efficiency. Understanding how accurate these machines are is crucial for industries relying on tight tolerances and high-quality outputs. This article explores the factors influencing CNC accuracy and the implications for production, helping readers grasp the importance of precision in their operations. For businesses requiring reliable and precise machining services, OurPCB CNC Machining offers solutions that meet the highest standards in manufacturing.
Overview of CNC Machine Accuracy
CNC machine accuracy refers to the ability of CNC machines to produce parts within specified tolerances. Precision impacts the overall quality and reliability of manufactured products. Several factors influence this accuracy, including machine quality, maintenance, tooling, and environment.
Key Factors Affecting Accuracy
- Machine Construction Quality: Sturdy and stable construction reduces vibrations and improves performance. High-quality materials improve structural integrity.
- Calibration: Regular calibration ensures the CNC machine operates at specified tolerances. Inaccurate calibration leads to deviations in output.
- Tooling: Tool wear affects precision. Regular inspection and timely replacement of cutting tools maintain accuracy in operations.
- Environmental Conditions: Temperature fluctuations and humidity levels can influence machine performance. Stable conditions support optimal functioning.
- Operator Skill: Trained operators manage machine settings and processes efficiently. Inexperienced handling can result in programming errors that compromise accuracy.
Measurement of Accuracy
Manufacturers often use metrics like dimensional accuracy and repeatability to evaluate CNC accuracy. Dimensional accuracy measures how closely a part’s dimensions match the intended design. Repeatability assesses the machine’s ability to reproduce the same part multiple times within specified tolerances.
Expected Accuracy Levels
CNC machine accuracy varies by type and specifications. Typical accuracy levels for standard CNC machining range from ±0.001 inches (0.025 mm) to ±0.0005 inches (0.0127 mm). Advanced CNC systems can achieve even tighter tolerances, down to ±0.0001 inches (0.00254 mm) in specialized applications.
Consistent accuracy in CNC machining is crucial for industries requiring high precision, such as aerospace, automotive, and medical devices. Understanding the factors that contribute to CNC machine accuracy helps companies optimize their production processes.
Factors Affecting CNC Machine Accuracy
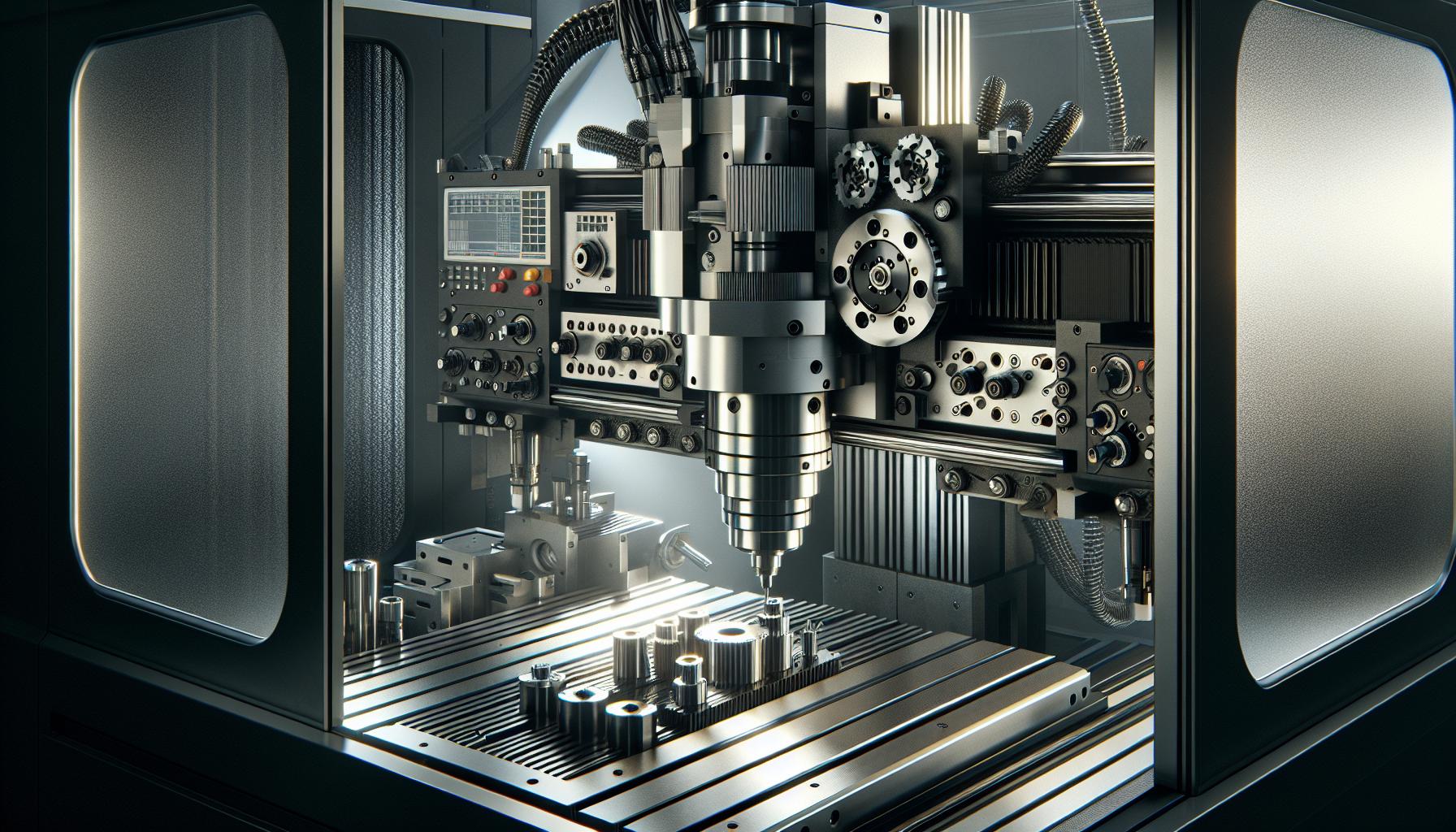
Several factors impact the accuracy of CNC machines. Understanding these elements is essential for achieving high precision in manufacturing processes.
Machine Construction
Machine construction significantly influences accuracy. Sturdy frames and high-quality components minimize vibrations and deflections during operation. Proper alignment of linear guides and ball screws assures precise movement. Materials used in construction, like cast iron or aluminum, affect thermal stability, impacting long-term performance.
Tool Performance
Tool performance affects machining accuracy through wear and geometry. Sharp tools yield cleaner cuts, enhancing dimensional accuracy. Dull tools introduce errors, leading to inconsistencies in the finished product. Additionally, choosing appropriate tool materials, such as carbide for harder materials, ensures efficiency and reduces wear.
Environmental Conditions
Environmental conditions play a vital role in CNC machine accuracy. Temperature fluctuations can cause expansion or contraction of machine parts, leading to dimensional changes. Humidity levels may also affect the material being machined. Maintaining a stable temperature and low humidity in the machining environment promotes consistent accuracy.
Measuring CNC Machine Accuracy
Understanding how to measure CNC machine accuracy is essential for maintaining high production standards. Accuracy measurements ensure that machines perform according to specified tolerances, which is crucial for industries requiring precision.
Common Measurement Methods
CNC machine accuracy can be assessed using several measurement methods.
- Laser Interferometry: This method measures distance with high precision using laser beams. It detects deviations in position in real-time, offering immediate feedback for adjustments.
- Ballbar Testing: A ballbar measures circular motion accuracy by moving along a predetermined circular path. It helps identify errors in axis movement and can diagnose alignment issues.
- Gage Blocks: Gage blocks are precise lengths that assess dimensional accuracy. By measuring a workpiece against gage blocks, operators can determine variances from expected dimensions.
- CMM (Coordinate Measuring Machine): A CMM measures the physical geometrical characteristics of an object. Operators can probe materials in three-dimensional space to report on accuracy and dimensions.
Tolerance Standards
Tolerance standards define the permissible limits of variation in a manufactured part. These standards are critical for ensuring consistent product quality.
- ISO (International Organization for Standardization): ISO publishes standards outlining tolerance levels for different manufacturing processes, including CNC machining.
- ASME (American Society of Mechanical Engineers): ASME provides guidelines on geometric dimensioning and tolerancing. Their standards ensure parts fit and function properly in assemblies.
- ANSI (American National Standards Institute): ANSI sets forth tolerances that apply to manufacturing both domestically and internationally, facilitating quality and uniformity across sectors.
Manufacturers aim for tight tolerances, typically within ±0.001 inches to ±0.0001 inches. Accurate adherence to these standards helps minimize defects and enhances product reliability.
Real-World Applications of CNC Machine Accuracy
CNC machine accuracy plays a critical role in several key industries, impacting product quality and operational efficiency.
Aerospace Industry
CNC machines in the aerospace industry require exceptional accuracy due to stringent safety and performance standards. Parts such as turbine blades, fuselage components, and intricate assembly brackets demand tolerances often within ±0.0001 inches. The capability of CNC machines to maintain such precision ensures that parts fit perfectly, enhancing overall aircraft performance and safety. Manufacturers use CNC technology to produce lightweight, complex geometries that meet rigorous specifications while optimizing material usage.
Automotive Industry
CNC machines are integral to the automotive industry, where precision directs everything from engine components to body panels. The accuracy of CNC machining influences the alignment and functionality of hundreds of parts in a vehicle. Tolerances in automotive manufacturing frequently range from ±0.001 inches to ±0.005 inches, depending on the component. CNC technology facilitates high-volume production with consistency and repeatability, enabling manufacturers to meet demand while maintaining quality. Additionally, CNC machining supports rapid prototyping, allowing for iterative design adjustments before mass production, ultimately leading to better-performing vehicles.
Conclusion
CNC machine accuracy is a cornerstone of modern manufacturing. Its ability to deliver precise and consistent results directly impacts product quality and operational efficiency. Understanding the various factors that influence accuracy helps manufacturers optimize their processes and maintain high standards.
With the right machine construction, proper calibration, and skilled operators, CNC machines can achieve remarkable tolerances. Industries like aerospace and automotive rely on this precision to meet stringent safety and performance requirements. By prioritizing accuracy and adhering to established tolerance standards, manufacturers can improve reliability and reduce defects in their products. Embracing CNC technology not only streamlines production but also paves the way for innovation and excellence in manufacturing.
Frequently Asked Questions
What is the impact of CNC machines on manufacturing?
CNC machines greatly enhance manufacturing by providing high precision and efficiency. They ensure consistent quality and accuracy, which is critical for industries requiring tight tolerances. CNC technology helps streamline production processes, reducing waste and time, enabling manufacturers to meet high standards and customer expectations.
How do I measure CNC machine accuracy?
CNC machine accuracy can be measured using methods like laser interferometry, ballbar testing, gage blocks, and coordinate measuring machines (CMM). Each method provides insights into different aspects of the machine’s performance, helping identify areas for improvement and ensuring high production standards are maintained.
What factors influence CNC accuracy?
CNC accuracy is influenced by various factors, including machine construction quality, calibration, tooling, environmental conditions, and operator skill. Sturdy frames and high-quality components reduce vibrations, while sharp tools enhance performance, contributing to overall machining precision.
What are common accuracy levels for CNC machines?
CNC machines typically achieve accuracy levels ranging from ±0.001 inches to ±0.0001 inches. Advanced systems are capable of tighter tolerances, which is crucial for industries such as aerospace, automotive, and medical devices that demand high-quality outputs.
Why is CNC machine accuracy important in specific industries?
In industries like aerospace and automotive, CNC machine accuracy is vital for producing components that meet strict safety and performance standards. Ensuring precision minimizes defects and enhances product reliability, making it essential for high-volume production and rapid prototyping needs.
What tolerance standards are important for CNC machining?
Important tolerance standards for CNC machining include those set by organizations like ISO, ASME, and ANSI. These standards define permissible limits of variation in manufactured parts, enabling manufacturers to produce high-quality products with minimal defects while maintaining compliance in their operations.