Ordering custom CNC parts can be a game-changer for businesses looking to improve their manufacturing processes. With precision and quality at the forefront, understanding the key considerations before placing an order is crucial. This article dives into essential factors like material selection, design specifications, and vendor reliability, ensuring that readers make informed decisions for their projects.
Key Considerations When Ordering Custom CNC Parts
Selecting the right specifications is crucial when ordering custom CNC parts. Each project requires precise measurements, tolerances, and features tailored to its unique demands. Clearly define dimensions, surface finish requirements, and any functional features necessary for optimal performance.
Choosing materials impacts both the quality and functionality of CNC parts. Common materials include aluminum, steel, and plastic. Each material behaves differently under various conditions, so understanding the end-use of the component is essential.
Vendor reliability plays a vital role in the success of the ordering process. Investigate the vendor’s experience, customer reviews, and certifications. A trustworthy vendor ensures product consistency and timely delivery, which reduces the risk of project delays.
Cost considerations also affect the ordering process. Assess the pricing structures of multiple vendors to find a balance between quality and cost. Sometimes, higher initial costs can lead to greater long-term savings through durability and reduced maintenance.
Prototyping is an effective strategy for validating designs before full-scale production. Ordering a prototype allows for testing functionality, fit, and performance. It reduces risks associated with production errors, ensuring the final product meets specifications.
Communication is key throughout the process. Maintain clear and open dialogue with the vendor to address any issues and clarify any uncertainties. Providing detailed information about the project can prevent misunderstandings and align expectations.
By focusing on these essential aspects, ordering custom CNC parts becomes a streamlined and effective process, ensuring high-quality results for any project.
Understanding CNC Machining
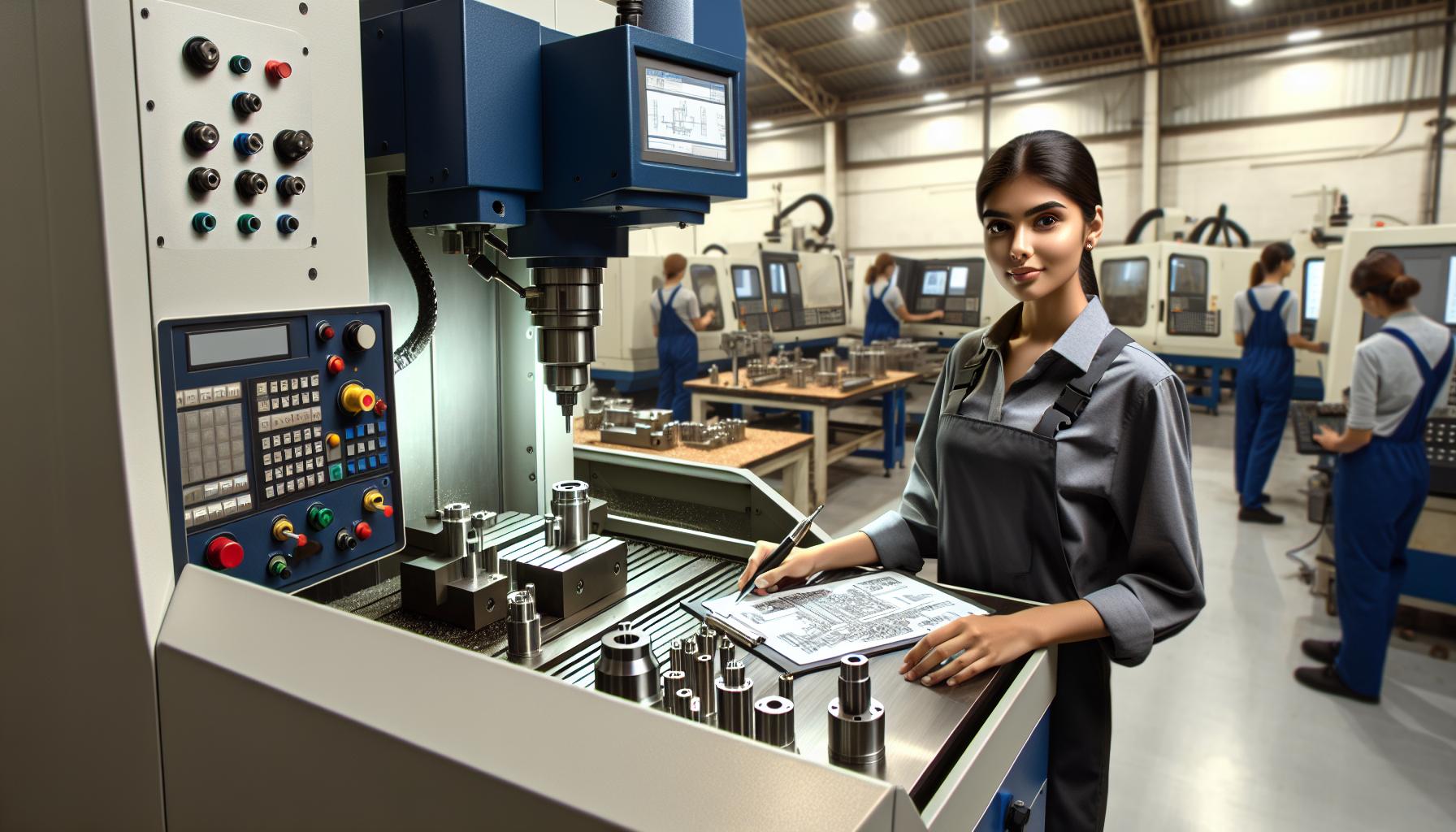
CNC machining involves a process where computer-controlled machines produce precision parts from various materials. It plays a critical role in modern manufacturing, ensuring accuracy and repeatability in production.
Overview of CNC Machining
CNC, or Computer Numerical Control, refers to the use of software to control machine tools. This technology allows for the automation of several machining processes, such as drilling, milling, and turning. By programming the movements and operations, CNC machines reduce human error and improve the consistency of finished products. The ability to create complex geometries while maintaining tight tolerances sets CNC machining apart from traditional methods.
Types of CNC Machines
CNC machining encompasses several types of machines, each suited for specific tasks:
- CNC Mills: These machines use rotary cutters to remove material from a workpiece. They can produce a wide range of shapes and are effective for complex designs.
- CNC Lathes: Lathes rotate the workpiece against a fixed cutting tool. They excel in creating cylindrical parts, such as shafts and fittings.
- CNC Plasma Cutters: These devices use high-velocity jets of ionized gas to cut through materials, particularly metals. They provide speed and efficiency for sheet metal fabrication.
- CNC Waterjet Cutters: Waterjet machines use high-pressure water mixed with abrasive materials to cut through various substances, including metals and plastics. They minimize heat-affected zones, preserving material integrity.
- CNC Routers: Routers are ideal for cutting softer materials, such as wood, plastics, and foam. They are commonly used in sign-making and furniture production.
Understanding these machine types enables better decision-making when ordering custom CNC parts, ensuring alignment with project requirements.
Material Selection
Selecting the right material for custom CNC parts is crucial for ensuring performance and durability. The choice of material affects the part’s functionality, appearance, and cost.
Common Materials for CNC Parts
- Aluminum: Lightweight and corrosion-resistant, aluminum is ideal for aerospace and automotive applications. It’s easy to machine and provides good thermal conductivity.
- Steel: Known for its strength and durability, steel is widely used in construction and heavy machinery. It offers excellent wear resistance, making it suitable for high-load applications.
- Plastic: Common plastics used include ABS, nylon, and polycarbonate. These materials are often utilized for prototypes and low-stress applications due to their lightweight and cost-effectiveness.
- Titanium: Strong and lightweight, titanium is resistant to corrosion and suitable for demanding industries like medical and aerospace. Its machining process requires specialized techniques due to its toughness.
- Mechanical Properties: Consider the strength, hardness, and flexibility of materials. Different projects require different mechanical characteristics to meet functional requirements.
- Environmental Resistance: Evaluate exposure to factors like moisture, chemicals, and extreme temperatures. Selecting materials with appropriate resistance can improve longevity.
- Cost Considerations: Balance material quality with project budget. While high-performance materials may offer better results, they often come at a higher cost.
- Machinability: Some materials are easier to machine than others. Assessing the machinability helps in determining production timelines and potential costs.
- Weight Restrictions: In applications where weight is a concern, selecting lightweight materials can improve overall efficiency. This factor is critical in industries like aerospace and automotive.
Making informed choices about material selection contributes significantly to the success of custom CNC parts, impacting performance and overall project viability.
Design Specifications
Design specifications play a critical role in the creation of custom CNC parts. Clearly defined specifications ensure the final product meets the intended purpose while maintaining the required quality and precision.
Importance of Detailed Drawings
Detailed drawings are essential for successful CNC part manufacturing. Drawings should include precise measurements, annotations, and notes on material finishes. Clarity in drawings prevents misinterpretation, minimizing errors during production. Accurate drawings lead to better alignment between the design intent and the final result, thereby enhancing overall project success.
Tolerances and Specifications
Tolerances define the allowable variation in dimensions, significantly impacting part functionality. They ensure parts fit together as intended, especially in assemblies. Proper tolerance specifications account for factors such as material behavior during machining and environmental conditions. Clear communication of tolerances helps manufacturers achieve the necessary accuracy, leading to effective performance in end-use applications. Specifying tolerances in decimal or fractional format provides clarity and precision, crucial for maintaining the integrity of the final product.
Cost Analysis
Cost plays a significant role when ordering custom CNC parts. Understanding the factors influencing costs and effective budgeting strategies helps maintain project alignment with financial resources.
Factors Affecting Cost
- Material Selection: The choice of material directly impacts the overall price. Common materials like aluminum and steel typically come at different costs per unit, affecting the total expenditure.
- Complexity of Design: More intricate designs require additional machining time and resources, elevating labor costs. Simple parts generally incur lower production expenses.
- Quantity Ordered: Bulk orders often result in lower per-unit costs due to economies of scale. Smaller orders may lead to higher prices per unit due to setup costs not being spread over a larger quantity.
- Tolerances and Specifications: Stricter tolerances necessitate more precise machining, which typically incurs higher costs due to the need for specialized equipment or additional processing time.
- Vendor Pricing Strategies: Different vendors implement varying pricing models based on their operational costs, market demand, and production capabilities. Evaluating multiple quotes ensures competitive pricing.
- Establish Clear Objectives: Define the project scope, including intended use, required quantities, and timetable. This sets the groundwork for an accurate budget.
- Include All Expenses: Factor in not just the manufacturing costs but also shipping, taxes, and potential modifications. Comprehensive budgeting prevents unexpected financial burdens.
- Prioritize Quality: Balance quality and cost effectively. Investing in high-quality parts may result in reduced long-term maintenance and replacement costs.
- Monitor Vendor Payment Terms: Understand payment schedules offered by vendors. Negotiating favorable terms can aid in cash flow management and resource allocation.
- Review Historical Data: If available, analyze past projects for insights into cost patterns. Historical data can illuminate potential savings or necessary adjustments for future orders.
Supplier Selection
Choosing the right supplier for custom CNC parts is essential for ensuring quality and reliability. Working with a reputable custom CNC parts manufacturer can significantly impact the success of your project by offering advanced capabilities, consistent quality, and timely delivery. The selection process involves evaluating potential candidates based on experience, capabilities, and customer feedback.
Evaluating CNC Suppliers
Evaluating CNC suppliers requires thorough research and careful consideration of several key factors. First, check the supplier’s experience and expertise in the specific materials and processes needed for the project. Second, review customer testimonials and case studies to assess the supplier’s reliability and product quality. Third, consider the supplier’s capacity to handle the required order volume without sacrificing quality or lead times. Fourth, evaluate the technological capabilities of the supplier, including the type and condition of CNC machines used in production, as this impacts precision and efficiency. Fifth, assess the supplier’s certifications, such as ISO 9001, which indicate adherence to quality management standards.
Evaluation Factor | Description |
---|---|
Experience | Check the supplier’s history in the industry. |
Customer Feedback | Review testimonials and case studies. |
Production Capacity | Ensure they can meet desired order volumes. |
Technological Capabilities | Evaluate the types of machines and tools used. |
Certifications | Look for quality management certifications. |
Importance of Communication
Effective communication with suppliers significantly impacts project success. Clear communication ensures that both parties have a mutual understanding of specifications, expectations, and timelines. Providing detailed drawings and design documents is vital to convey specific requirements and prevent misunderstandings. Regular updates during the manufacturing process help to address issues promptly, keeping the project on track. Additionally, establishing a direct line of communication fosters a collaborative relationship, making it easier to resolve challenges and adapt to changes as needed.
Conclusion
Ordering custom CNC parts involves a careful balance of precision quality and cost-effectiveness. Businesses must prioritize material selection and detailed design specifications to ensure optimal performance. Finding a reliable vendor is key to maintaining consistency and timely delivery. Prototyping can significantly reduce the risks associated with production errors. Clear communication throughout the process helps align expectations and prevents misunderstandings. By considering these factors businesses can streamline their manufacturing processes and achieve successful outcomes with their custom CNC parts.
Frequently Asked Questions
What are custom CNC parts, and why are they important for businesses?
Custom CNC parts are machine-made components tailored to specific design and material requirements. They are crucial for businesses as they enhance manufacturing processes, ensuring precision, quality, and optimal performance in various applications.
How does material selection impact custom CNC parts?
Choosing the right material is essential for the performance, durability, and appearance of custom CNC parts. Common materials like aluminum, steel, plastic, and titanium each have unique characteristics that can affect functionality and cost, making informed selection vital.
What are key considerations when designing custom CNC parts?
Important design considerations include clear specifications, accurate measurements, and material finishing notes. Proper tolerances and detailed drawings are crucial to prevent errors and misinterpretations, ensuring the final product meets quality and functional standards.
How can businesses manage costs when ordering CNC parts?
Managing costs involves understanding factors like material choice, design complexity, and vendor pricing. Implementing effective budgeting strategies, prioritizing quality, and monitoring expenses help align project budgets with financial resources while ensuring high-quality outcomes.
Why is supplier selection important for custom CNC parts?
Choosing the right supplier is vital for ensuring the quality and reliability of CNC parts. Evaluating a supplier’s experience, production capacity, and customer feedback helps in making informed decisions that can lead to successful project execution.
What are the benefits of prototyping custom CNC parts?
Prototyping allows businesses to validate designs before full-scale production, reducing the risk of errors and ensuring that parts meet specifications. This step can identify potential issues early, saving time and costs during the actual manufacturing process.
How does CNC machining technology improve manufacturing?
CNC machining automates the production of precision parts using computer-controlled machines, improving accuracy and repeatability. This technology reduces human error and enhances product consistency, playing a critical role in modern manufacturing efficiency.